Setting Up The Supersonic Airflow
When the car is running at subsonic speeds, a lot of what is going to happen to Aussie Invader’s airflow can be predicted with some certainty as there is a lot of aerodynamic data available on cars running in this speed range. It is a lot more difficult to predict the actual airflow around the vehicle when it is travelling in the transonic speed range. When the car is transonic, some parts of the car are receiving subsonic airflow and some are receiving supersonic airflow at the same time.
This can result in turbulent airflow and general instability. Unfortunately, there is very little data available from land speed record cars on transonic airflow, and what there is has shown cars can become very unstable.
Data on supersonic airflow close to the ground is very scarce. Thrust SSC achieved Mach 1.02, 763 mph (1,223 km/h) but Thrust SSC was only in the supersonic range for a very short time, we will hopefully be there a lot longer.
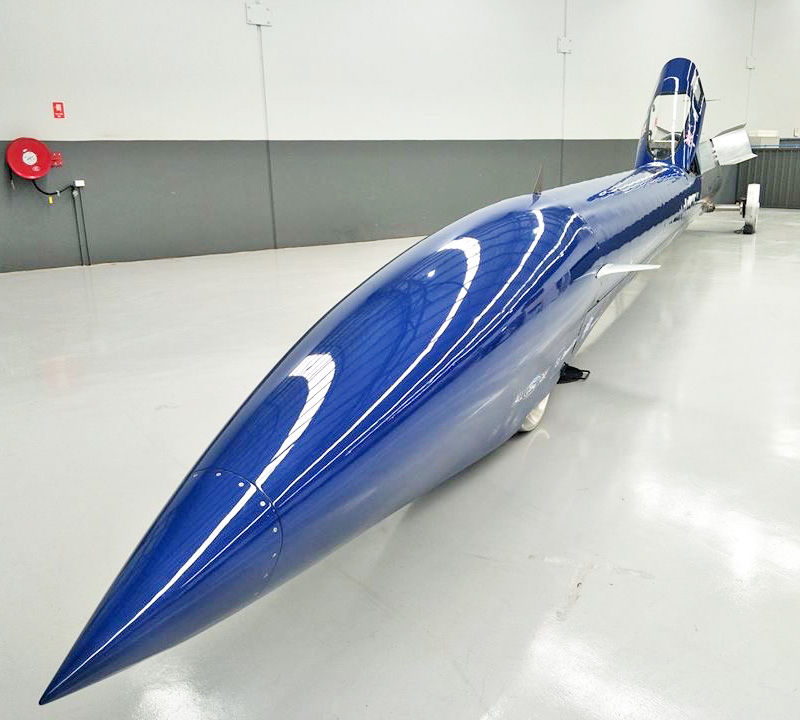
When Aussie Invader 5R reaches 1,000 mph it will have broken through the sound speed barrier, and will be travelling at close to 1.4 times the speed of sound, (Mach 1.4). Since Aussie Invader 5R will be moving faster than the sound waves it creates, it actually leads the advancing wavefront. The car will pass by a stationary observer before the observer actually hears the sound it creates.
The “sonic boom” an observer will hear as it goes through the sound barrier and beyond is actually the sound of the shock waves crashing into each other.
Aircraft have travelled at supersonic speeds for over 60 years. However, the shock waves from an aircraft can dissipate in all directions, where as a car in contact with the ground is completely different and the shock waves reflected from the ground can potentially cause a lot of unwanted lift and drag issues.
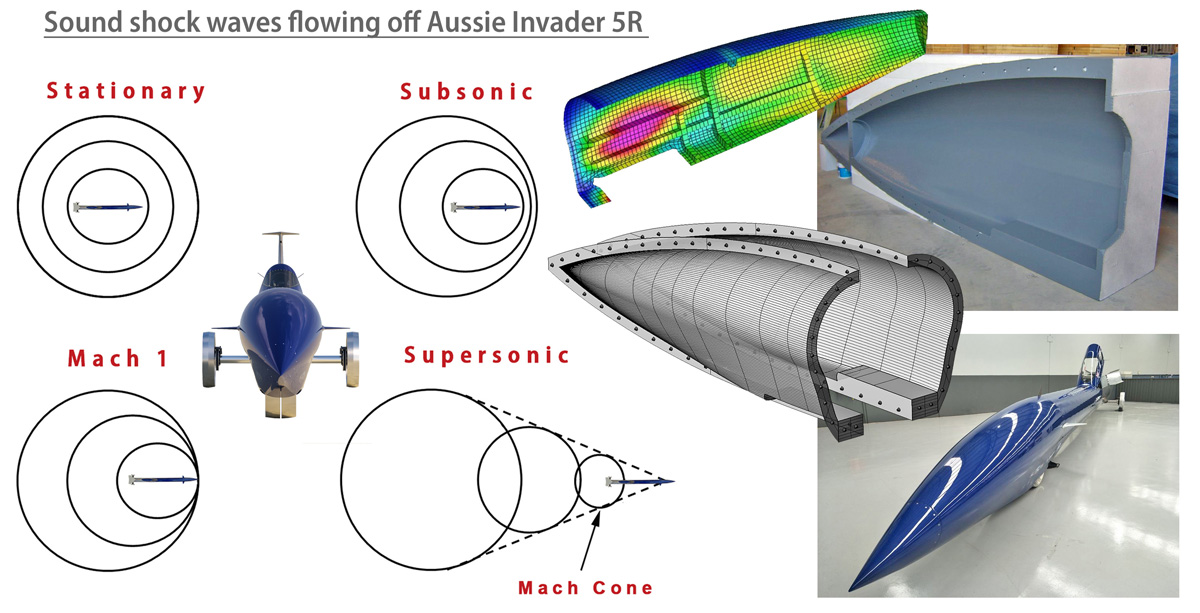
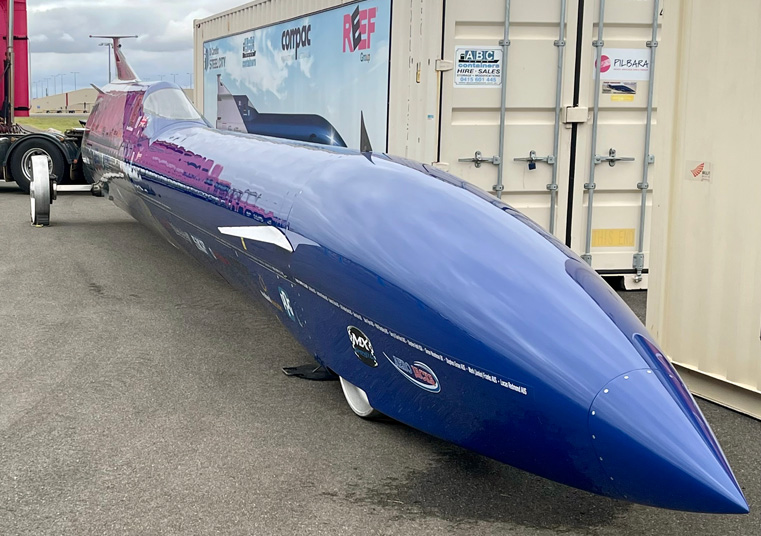
Running CFD (computational fluid dynamics) will help predict how a particular nose cone may perform against other designs. However, it will not determine every aspect of its performance. The safest and fastest nose cone will be determined with reference to data extracted from Aussie Invader’s preliminary speed trials. Methodical lift and stability testing over successively faster speeds will confirm a given nose profile’s ability to make record-breaking runs.
Beyond the speed of sound, air acts more like water, i.e. the air reacts as though it is very dense. Aussie Invader 5R’s nose will need to slice through the air and divert as much air to either side of the car as possible. In one sense, the nose cone must perform like the bow of a high-speed boat and cut through the air. A powerful boat with a poor bow design will not cut through the water and reach its potential. A good nose cone design must also minimise air travelling under the car.
At supersonic speeds, there will still be a large volume of high speed air which will induce shock waves which could bounce down the length of the car, creating lift. It a boat design, this is preferable, as it lifts a boat out of the water, allowing it to go faster. We will not want the nose of Aussie Invader 5R to create any real lift. If it does the car could flip. We need to keep a steady downward pressure on the nose and this will be achieved with the nose cones angled down design and adjustable canards (winglets) just behind the nose.
Swarbrick Yachts in Henderson, Western Australia completed the CNC profiling of our composite nose moulds. The design of this nose has taken several years to complete. We are currently producing a lighter and stronger nose in carbon fibre with the help of Aero Jacks in Jandakot, WA.
The Soto Group carried out our initial computational fluid dynamics (CFD) in NSW and Perth. Our nose is made from carbon fibre. It is designed to minimise lifting moments and can withstand the extreme forces and heat generated by a car travelling at speeds up to Mach 1.4 (450 metres per second).
The nose and any supporting frame also need to be super strong. Otherwise, the extreme forces exerted on them could cause them to collapse or snap off completely, and then the car and driver would be really in the hands of the gods.